Achieving Quality in Light Weight Aluminum Spreading: Vital Tips and Techniques
In the realm of light weight aluminum spreading, top quality and accuracy are vital (casting aluminum illinois). The procedure of transforming liquified light weight aluminum right into elaborate and long lasting components calls for a thorough approach at every phase. From meticulously picking the right materials to developing putting strategies and making certain thorough ending up touches, accomplishing quality in light weight aluminum spreading requires a blend of knowledge and focus to information. As professionals in the area aim to excellent their craft, mastering a set of essential tips and techniques comes to be crucial. Allow's check out the crucial components that can boost light weight aluminum spreading from great to extraordinary, establishing the phase for unmatched outcomes and unrivaled craftsmanship.
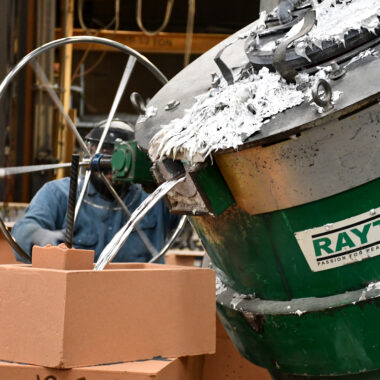
Products Option
Picking the ideal materials is extremely important in ensuring the success and quality of your aluminum casting projects. The option of products significantly impacts the final homes of the casted items, including strength, resilience, and overall quality. When choosing products for aluminum casting, it is essential to consider aspects such as the kind of light weight aluminum alloy, the desired mechanical buildings, and the spreading technique being utilized.
Aluminum alloys are frequently made use of in spreading due to their lightweight nature and superb mechanical residential or commercial properties. The selection of the specific alloy relies on the application needs, with choices ranging from high-strength alloys suitable for architectural elements to corrosion-resistant alloys for marine settings. Recognizing the features of various aluminum alloys is crucial for selecting one of the most ideal one for your project.
In addition, the spreading method used, whether it be sand casting, pass away casting, or financial investment spreading, likewise influences product selection. Each spreading technique has its very own demands in terms of material fluidness, thermal conductivity, and mold compatibility. By very carefully considering these aspects, you can guarantee that the products picked are customized to meet the certain needs of your light weight aluminum casting job.
Mold Prep Work
In the world of light weight aluminum spreading, the careful prep work of mold and mildews stands as a critical precursor to the real spreading process. It is critical to cleanse the mold and mildew completely to remove any type of dust, residue, or previous casting remnants that can endanger the new cast.
Following, applying an ideal mold covering is vital to help with the release of the cast light weight aluminum and improve the surface area finish of the part. The kind of finish made use of will depend upon aspects such as the complexity of the mold, the desired surface area coating, and the spreading product. In addition, correct venting and gating systems should be incorporated into the mold layout to permit for the smooth circulation of molten aluminum and prevent the development of air pockets or issues in the cast part.
Melting and Putting Strategies
To attain successful aluminum spreading, grasping reliable melting and putting techniques is critical for guaranteeing precise and high-quality results. The melting procedure is an important action in light weight aluminum spreading, where the metal is warmed to its liquid state. It is necessary to check the temperature closely to stop overheating, which can result in inadequate casting high quality. Making use of induction heating systems or gas-fired crucible heaters can supply browse around these guys accurate temperature level control and effective melting.
As soon as the light weight aluminum reaches the preferred liquified state, appropriate putting strategies must be utilized to move the metal right into the mold and mildews. The rate and uniformity of the put are vital consider accomplishing consistent dental filling of the mold and mildew tooth cavity and lowering the risk of problems like air entrapment or incomplete casting. Gravity putting, low-pressure spreading, or centrifugal spreading methods can be utilized based upon the specific demands of the job.
Air Conditioning and Solidification Control
Attaining accurate control over the air conditioning and solidification procedure is crucial in aluminum casting to maintain the stability and quality of the final casted products. Proper cooling and solidification control aid protect against issues such as porosity, warm rips, and shrinking that can endanger the mechanical residential or commercial properties of the casted aluminum components.
One important aspect of air conditioning check out here and solidification control is the style and placement of chills. Chills are metal things purposefully positioned in the mold and mildew to soak up warm swiftly from specific locations of the spreading, advertising uniform solidification and minimizing the likelihood of defects. In addition, regulating the air conditioning rate by changing the mold's product, layout, and the application of protecting coatings can influence the microstructure and mechanical properties of the last casting.
Additionally, monitoring and controling the cooling procedure with using thermocouples and computer system simulations allow for real-time adjustments to optimize air conditioning rates and solidification patterns. By applying these techniques, foundries can boost the quality and uniformity of their aluminum castings, meeting the rigorous demands of various markets.
Finishing and Quality Evaluation
Correctly implemented completing and quality assessment look at this now procedures are important in ensuring the general integrity and integrity of light weight aluminum castings, constructing upon the precise air conditioning and solidification control techniques utilized during the spreading procedure. Completing strategies such as grinding, sanding, and polishing aid remove excess product, smooth harsh surface areas, and boost the castings' final look. These processes not only improve the aesthetic appeal however additionally guarantee dimensional accuracy and performance.
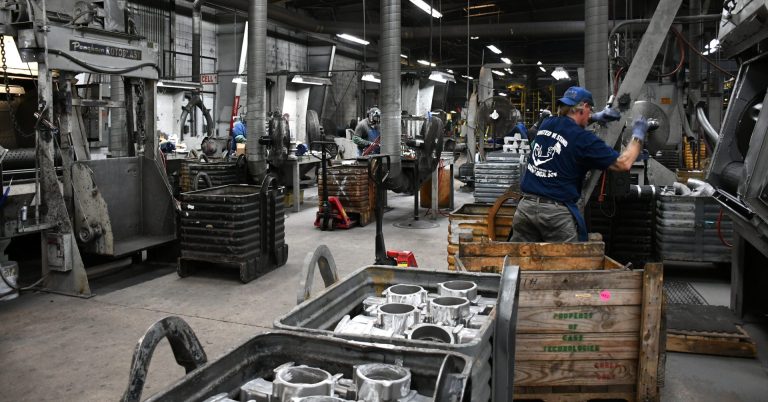
Final Thought
In final thought, achieving excellence in aluminum spreading requires mindful consideration of materials selection, meticulous mold prep work, precise melting and pouring strategies, reliable cooling and solidification control, in addition to thorough completing and top quality evaluation procedures. By following these crucial tips and techniques, suppliers can guarantee the manufacturing of high-quality aluminum castings that satisfy sector requirements and consumer assumptions.
When selecting materials for aluminum spreading, it is essential to think about variables such as the kind of light weight aluminum alloy, the wanted mechanical properties, and the casting method being utilized.
Additionally, the spreading approach employed, whether it be sand casting, die casting, or investment casting, likewise affects product choice.In the world of light weight aluminum spreading, the meticulous preparation of molds stands as a crucial forerunner to the real spreading process. Gravity pouring, low-pressure spreading, or centrifugal spreading approaches can be utilized based on the particular requirements of the project.
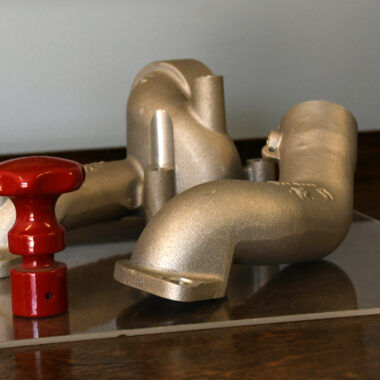